There are two categories of automatic badminton trainers: extremely expensive, and extremely limited in functionality. I’m attempting to build my own machine which has the features of a premium model such as being able to aim both horizontally and vertically, adjustable shot power, large capacity, and programmability, all while costing significantly less. My machine is almost entirely 3D printed with the except for some V-slot rails and steel shafts.
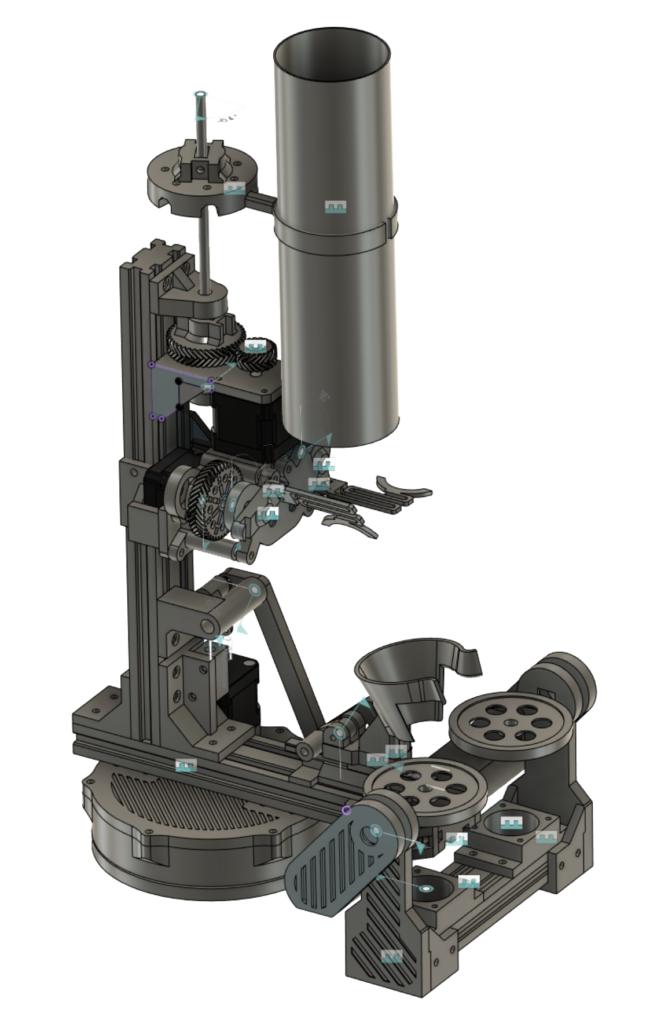
Unique Separator Design
One of the most challenging aspects of designing a shuttlecock launcher is separating the birdies one at a time from the barrel. Essentially all existing designs rely on multiple motors to move an arm up and down to pinch the birdie held by some tabs with one motion, then pull it down in another motion. I set out to try and accomplish this with one motor, while leaving clearance for the rotating top to switch between barrels of birdies.
Attempt #1
My first attempt was a gravity fed design using one motor and some gears. This one actually worked pretty well, but I didn’t like how large it was and it would often get clogged if too many birdies were on top due to the combined weight.
Attempt #2-5
My next 4 attempts were variations on the above design, also using one motor and some gears. I really wanted this one to work and I was pretty happy with it overall, but it was too unreliable. The dimensions of the moving arms had to be exact, and the rotation timing had to be very precise. This one also suffered from too much weight on top, limiting it’s capacity.
A problem with the gravity fed designs in general compared to the “plucking” designs, is that there’s no easy way to rotate and load in a fresh barrel of birdies without them all falling out.
Attempt #6
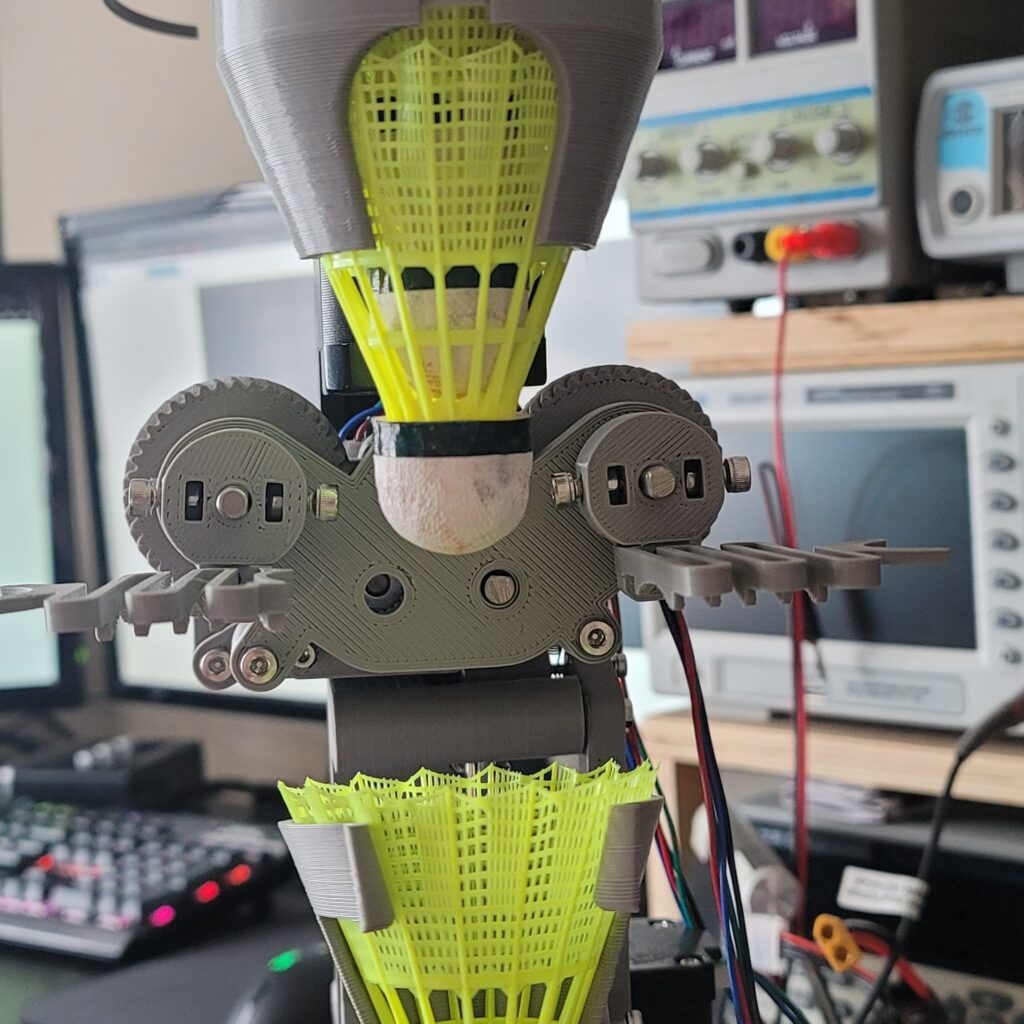
This is my current design. It took many iterations to proportion the arms correctly, but since they are flexible, it reliably grabs the birdie every time. The best part about this approach is that the arms can be positioned so that the rotating barrel has clearance allowing for it to be reloaded. As far as I know, this is the only existing plucking design which only requires one motor and is much simpler than the professional badminton trainers currently on the market.
Rotating Base
The design for the horizontal axis of my launcher was inspired by a robot arm from the 3D Printed Life YouTube channel. It makes use of a large ball bearing and a large plate sandwiched by two large thrust bearings. This worked excellently and is extremely smooth, resistant to axial load, and very quiet as well.
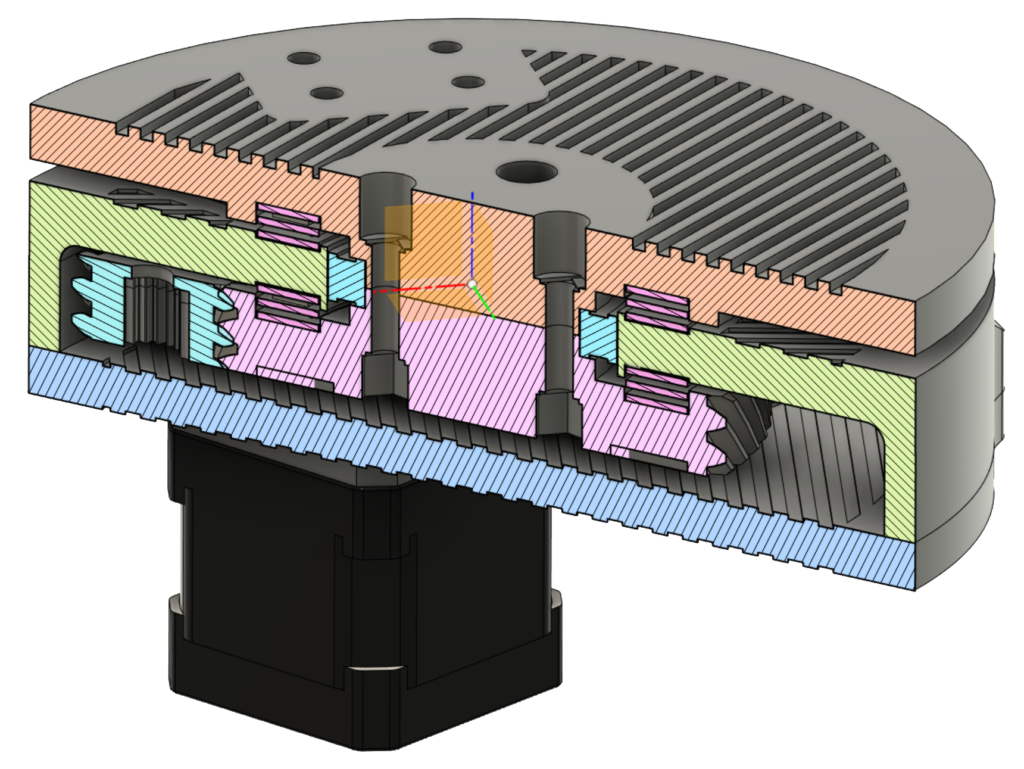
Rotating Barrel
While there is currently only one installed, the rotating shaft at the top of the machine has room for 7 barrels which should hold around 100 birdies. Since all the motion is driven by stepper motors, I have ideas to coordinate the motion of the rotating base with the barrel rotation to reduce shaking and vibrations. I may also switch between barrels every few shots to help balance the weight and keep the machine stable on its tripod mount.
What’s Next?
My next task will be to find a way to motorize the tilting axis for vertical aiming of shots. This is difficult because It’s been challenging to find a balanced motor/wheel assembly I can spin at high speeds with enough width to grip the birdies at different angles.
I’m also working on a PCB which will contain all the stepper motor drivers as well as a Bluetooth-enabled microcontroller to drive them and provide control through a phone application.
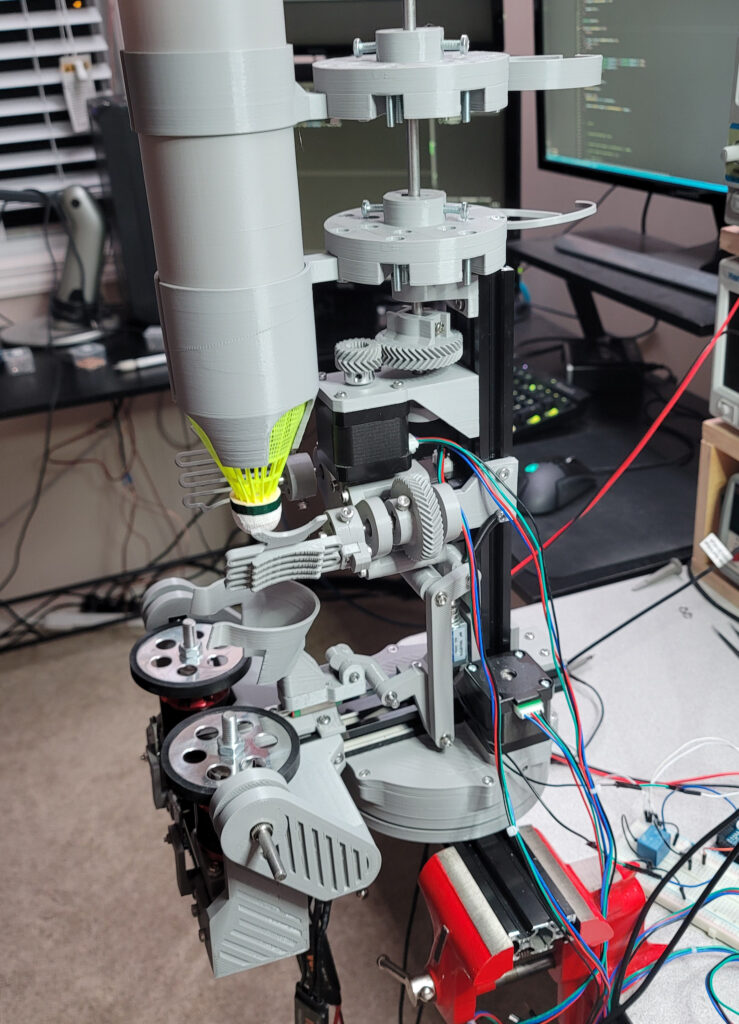